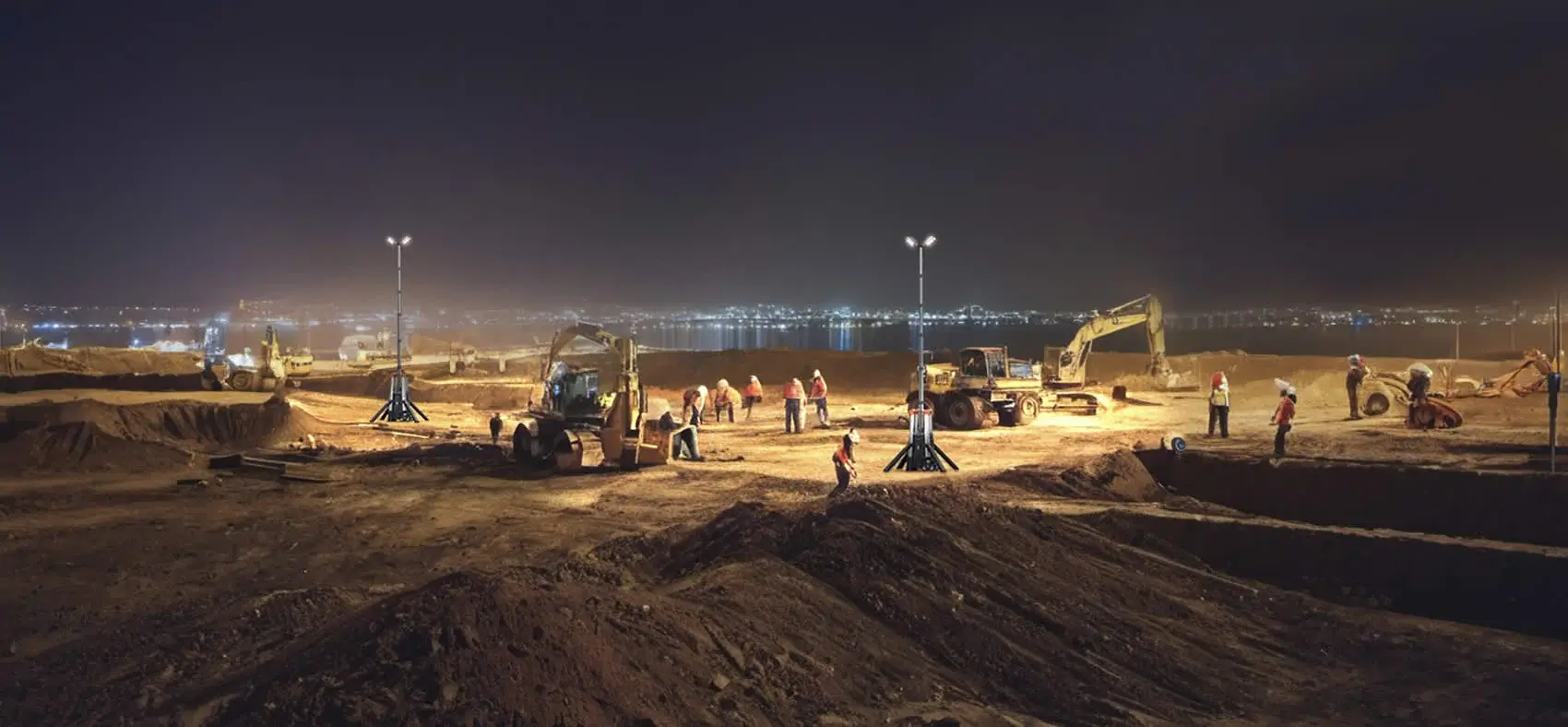
Professional lighting
Towers and portable lighting solutions.
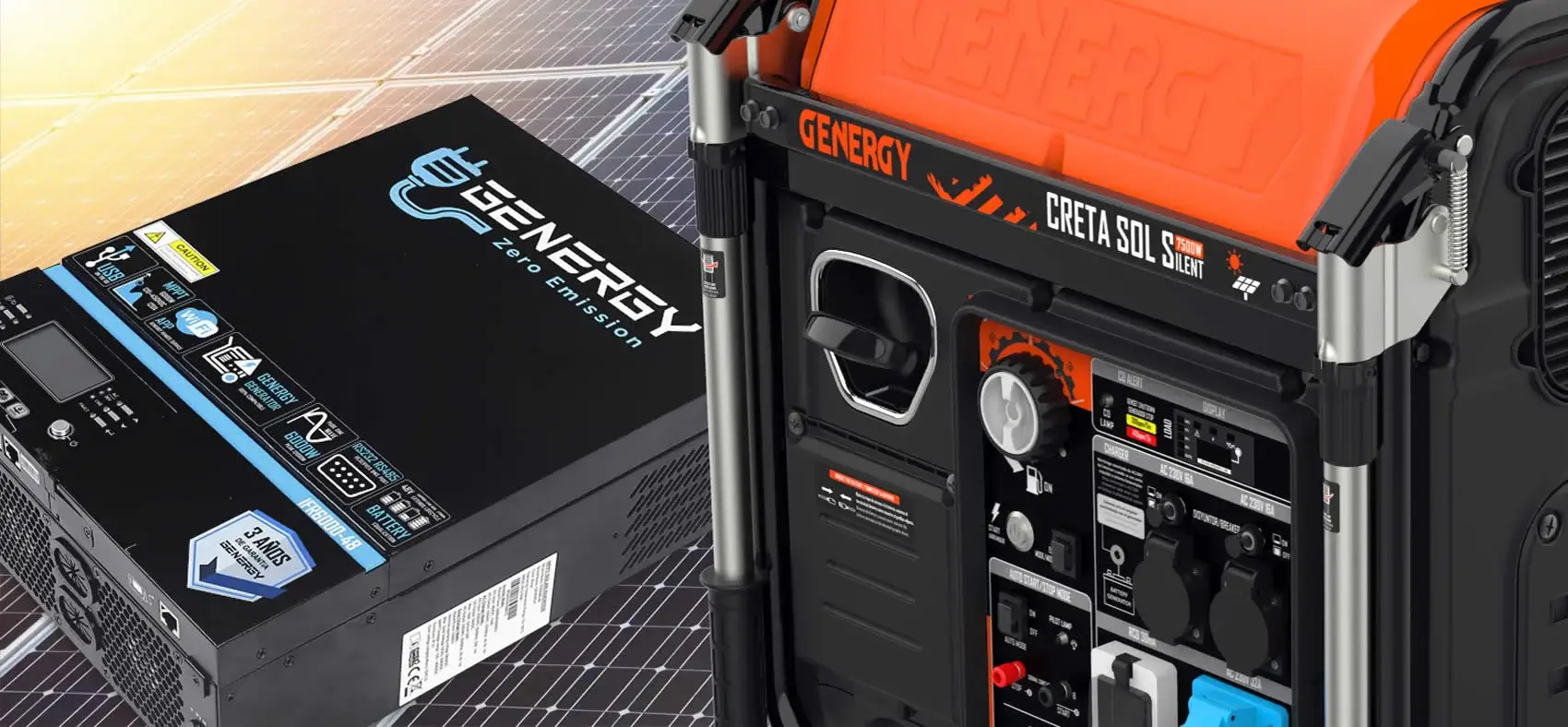
Kit backup generator + Inverter
Best price and compatibility guaranteed.
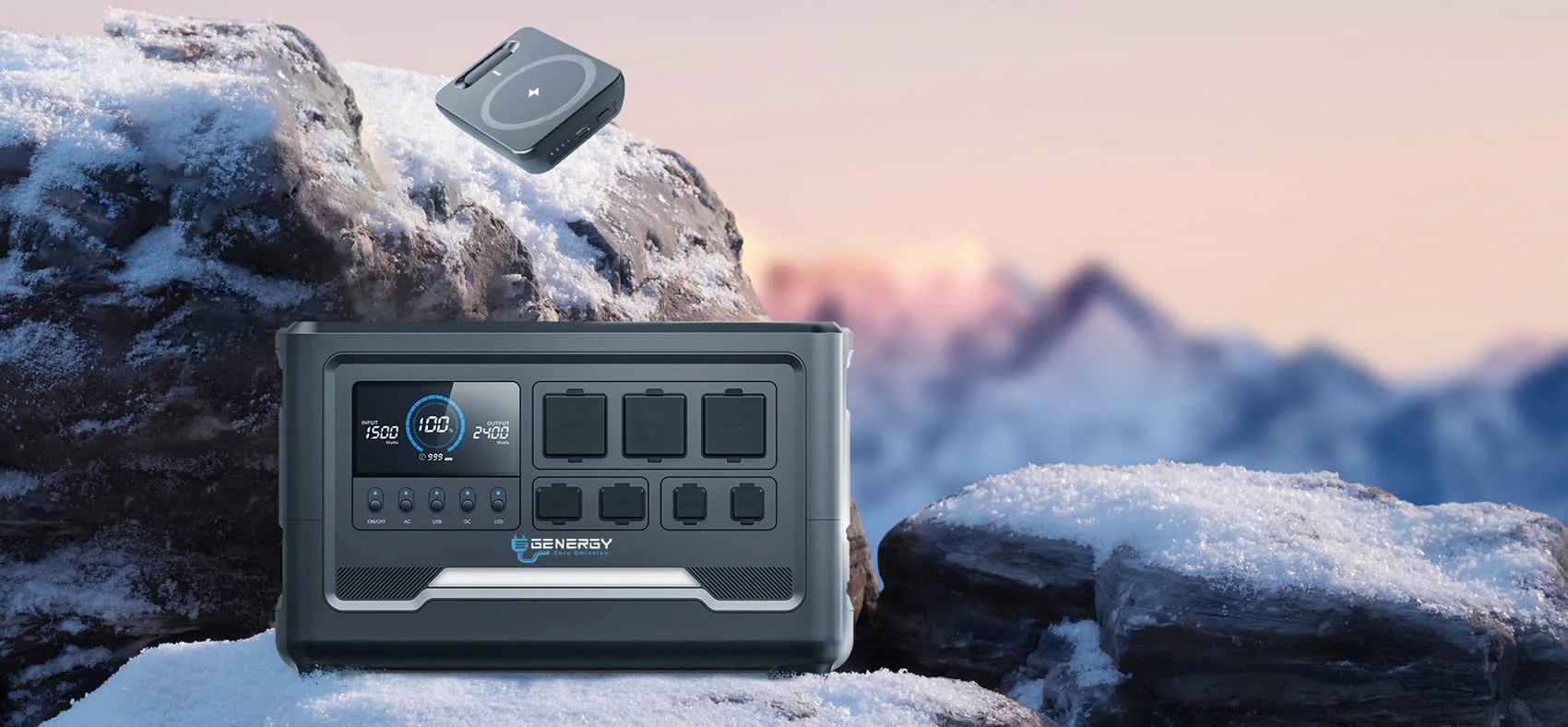
Power stations
From the most hobby to the most professional use
Fuel-free and noise-free
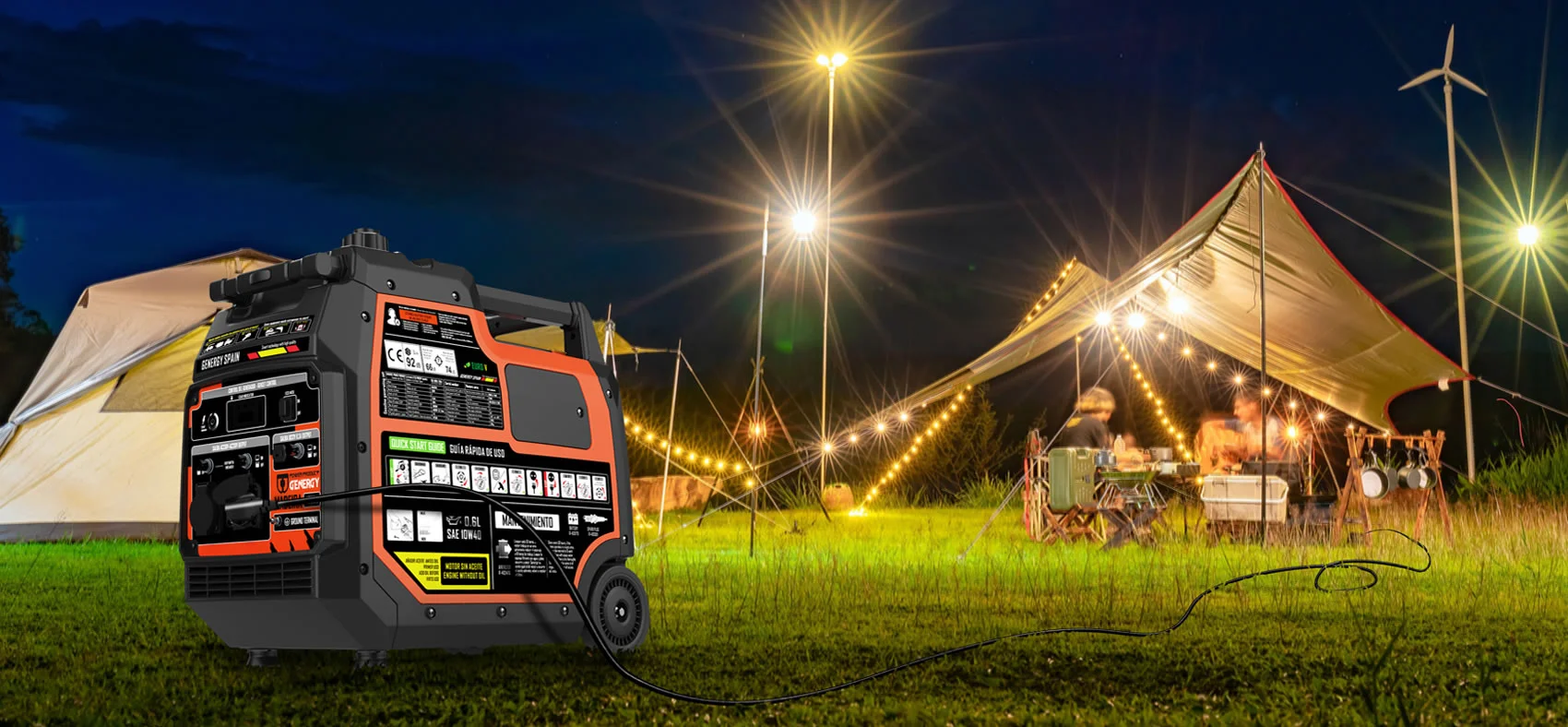
Gasoline generators
The widest range on the market.
Unbeatable quality-price ratio.
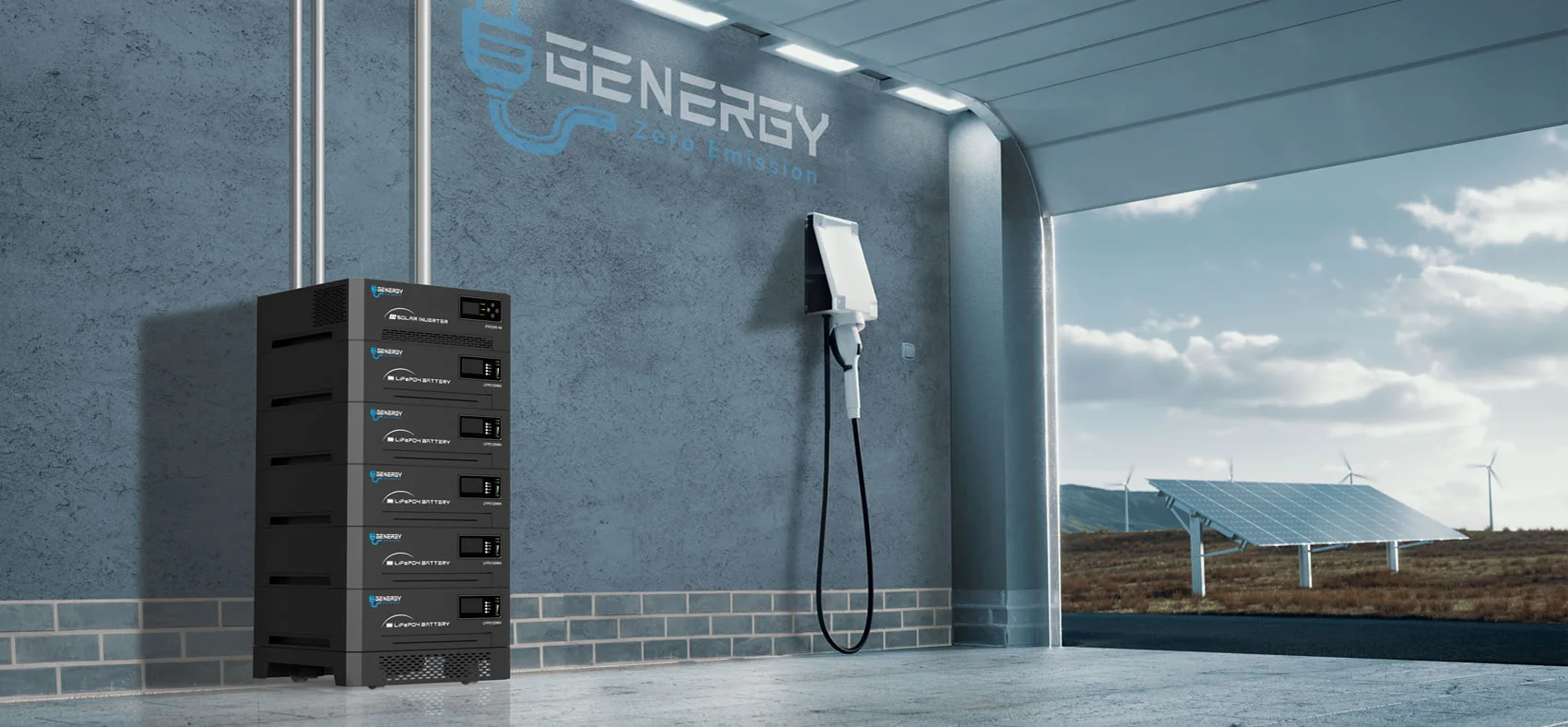
All-in-one photovoltaic system
Elegant design suitable for any environment.
No electrical cabinets required. Plug and play.
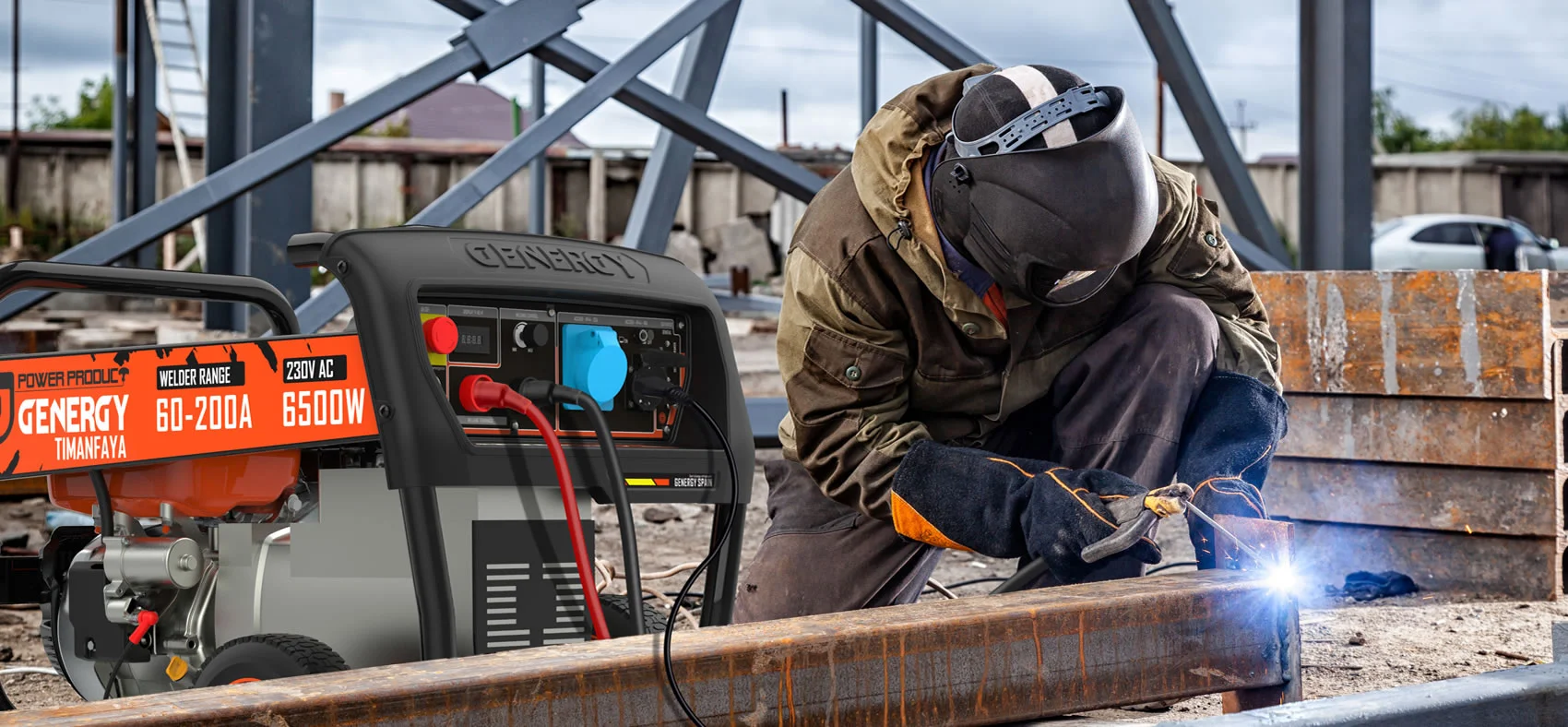
Autonomous machinery
Powerful and reliable motor welders.
Motor-compressors for pruning and mobile vehicles
High-pressure washers with AR pumps
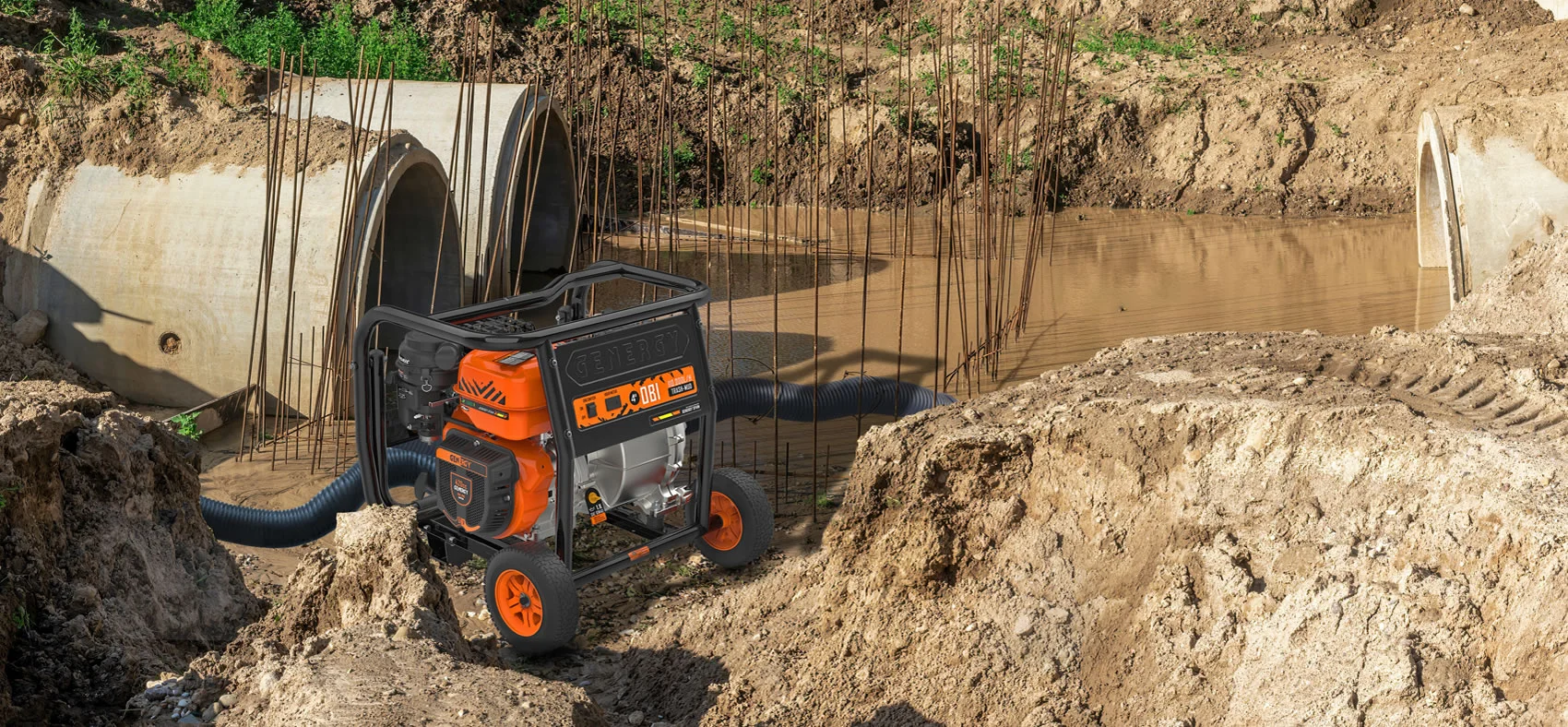
Range of motor pumps
Portable, flow, pressure, dirty water and anti-corrosion.
From 8000 to 150,000 L/H
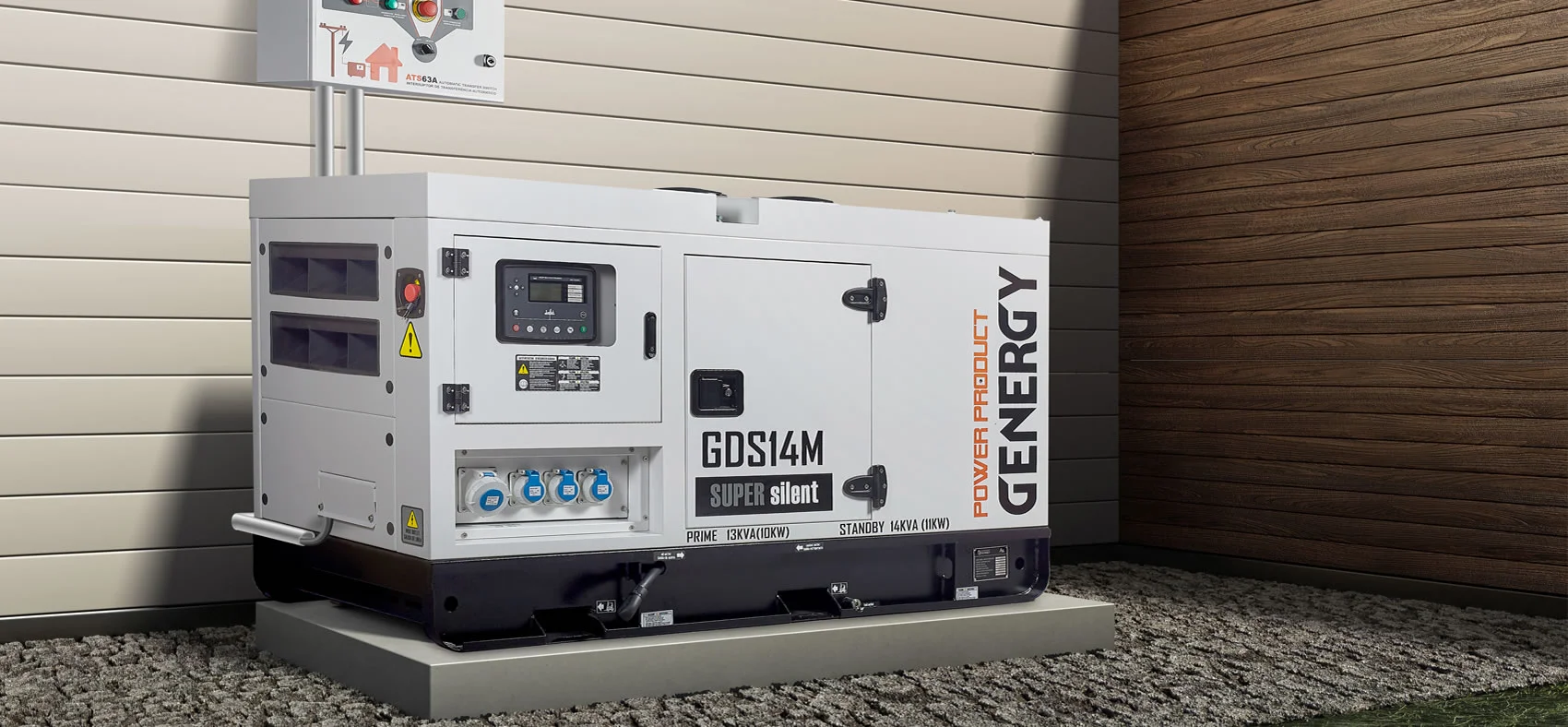
Diesel Generators 1500RPM
Water-cooled GENERGY engine
Power ratings from 10 to 350kVA
Featured
-
GENERATOR AZORES RC 10000W
Generator 12000W or more -
GENERATOR ELBA RC 5500W
Generator 3000W to 6kW -
CRETA SOL SILENT 7500W GENERATOR
Generator 6000W to 12kW -
GENERATOR CANDANCHÚ-S 7000W
Generator 3000W to 6kW -
GENERATOR FORMIGAL-S 7000W
Generator 3000W to 6kW -
GENERATOR STELVIO-S 18000W
Big Series Generator -
GENERATOR NATURA 8000 8500W
Generator 6000W to 12kW -
DIRECT 500-XL LIGHT TOWER
Professional Lighting
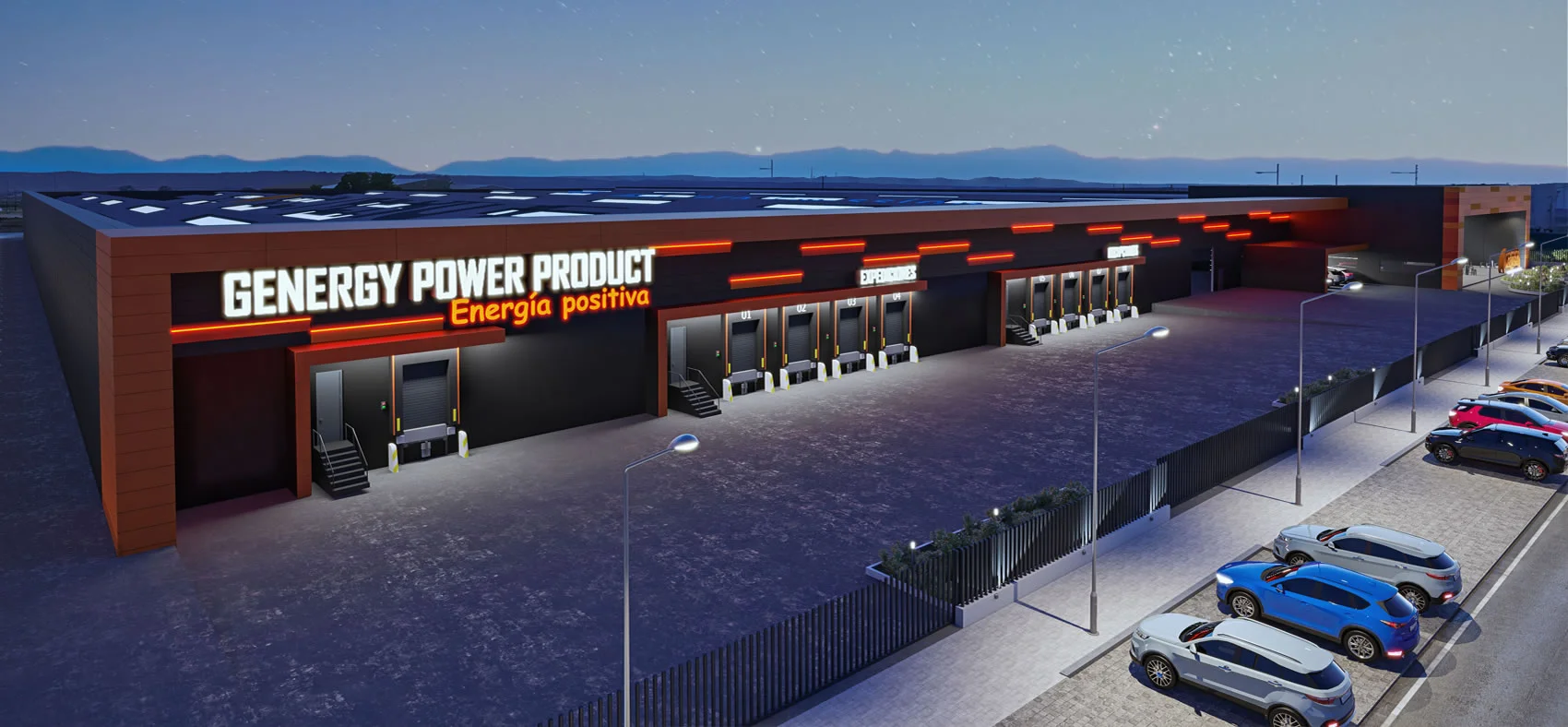
Our factory of ideas.
The positive energy of a motivated human team.
Creativity and passion, our hallmarks.
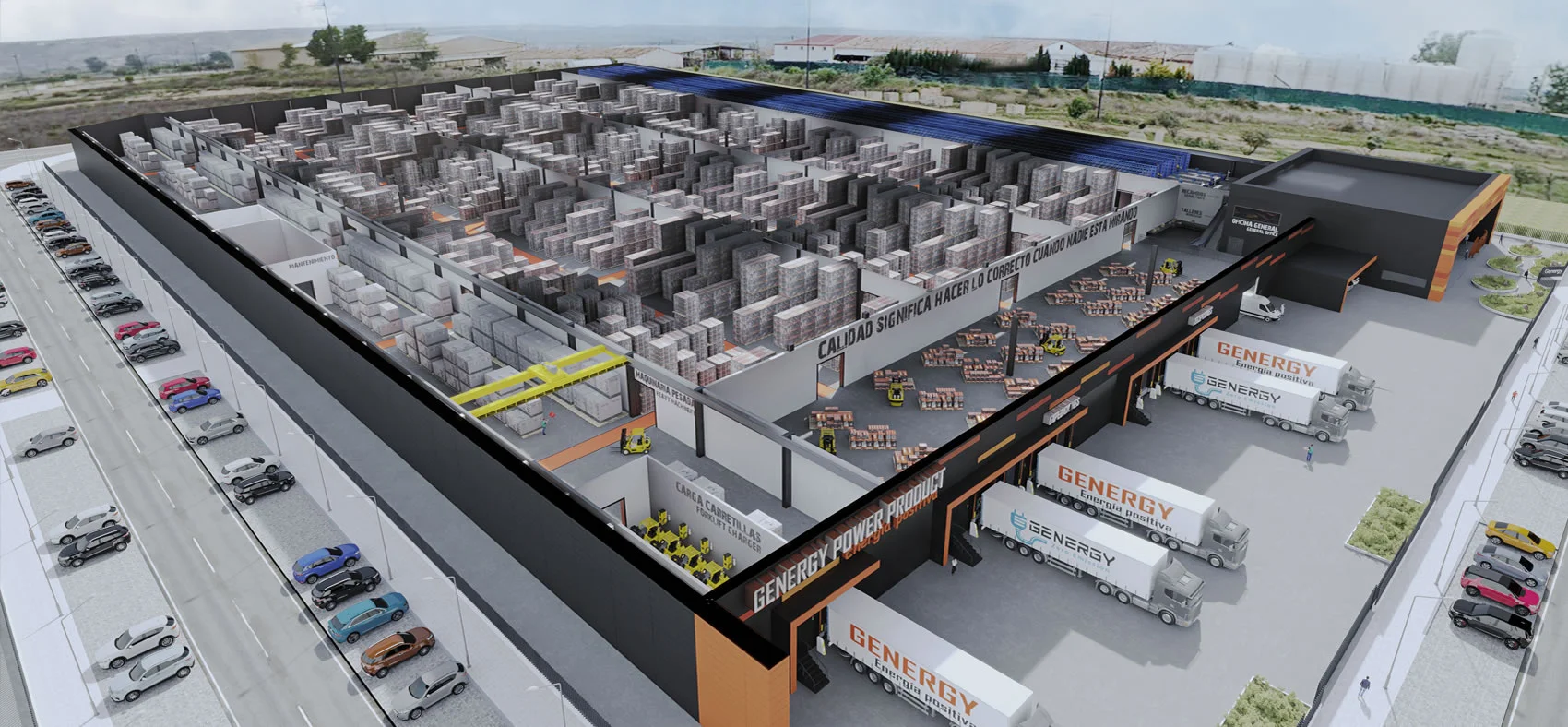
We are your best partner
The best facilities at the service of our customers.
The largest stock of portable generators in Europe.
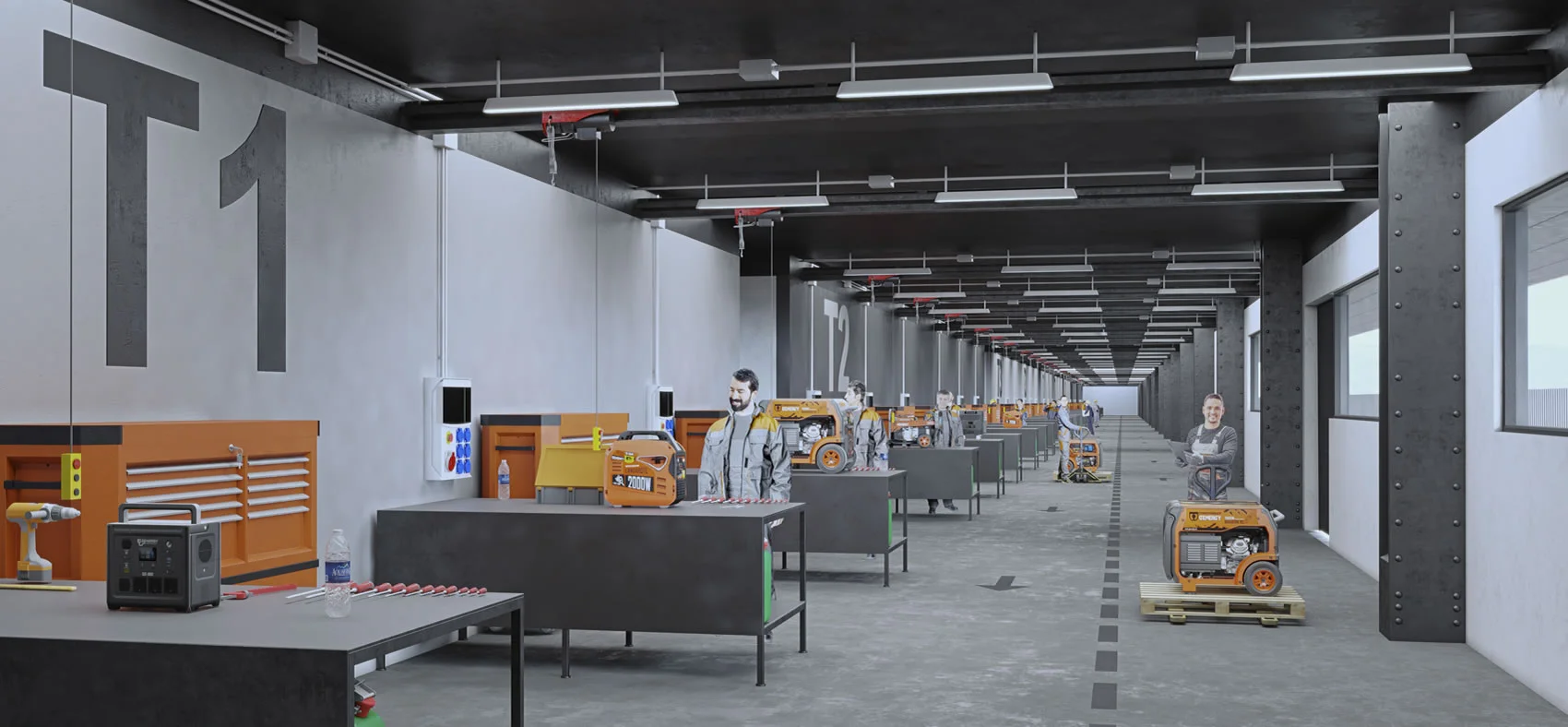
After-sales service as our flagship
Fully equipped workshops to assist with any unforeseen event.
Mechanics trained and specialized in our product line.
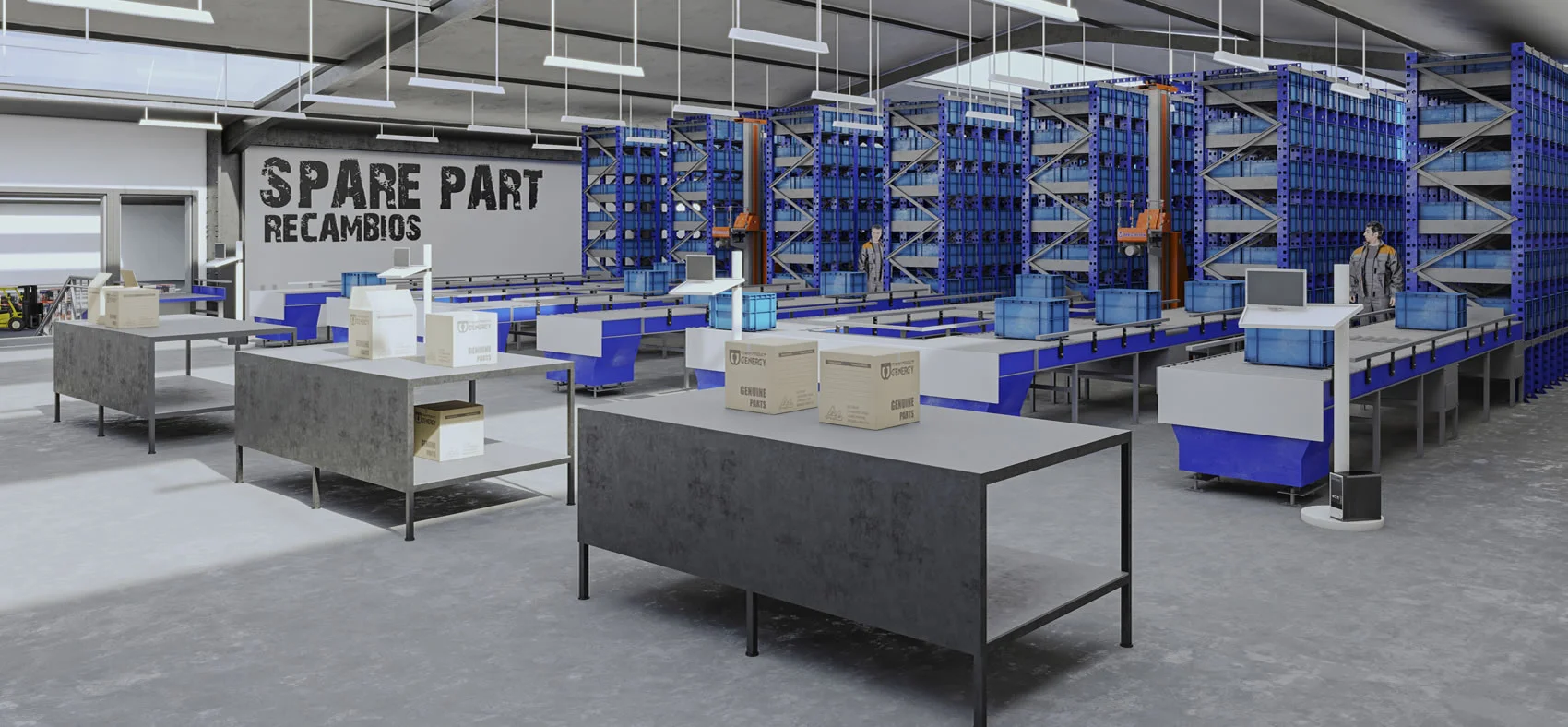
If it is GENERGY, spare parts are available.
More than 5,000 references in stock with delivery within 24/48 hours
Human team specialized in the area of spare parts
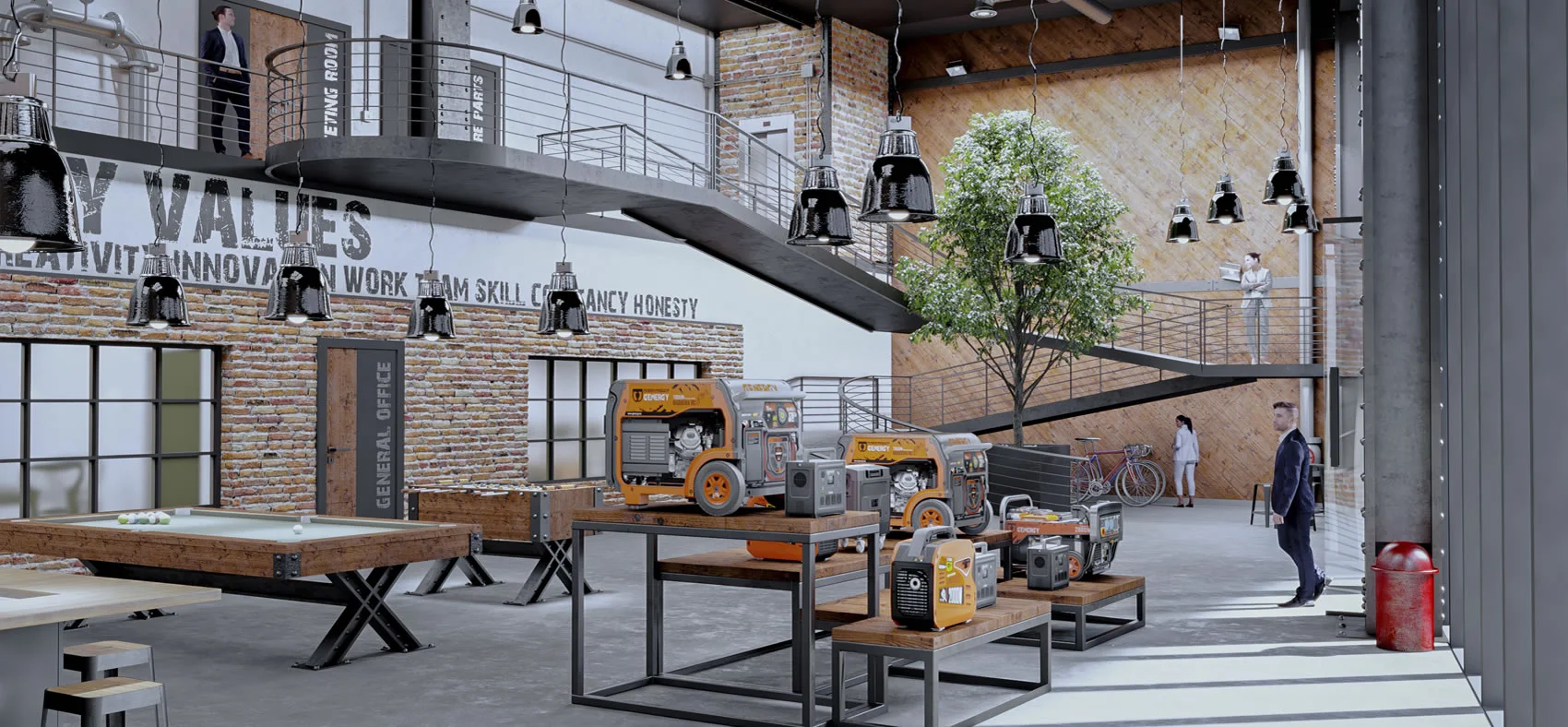
Multipurpose common areas.
VIP meeting areas for distributors and clients.
Permanent explosion of our products.
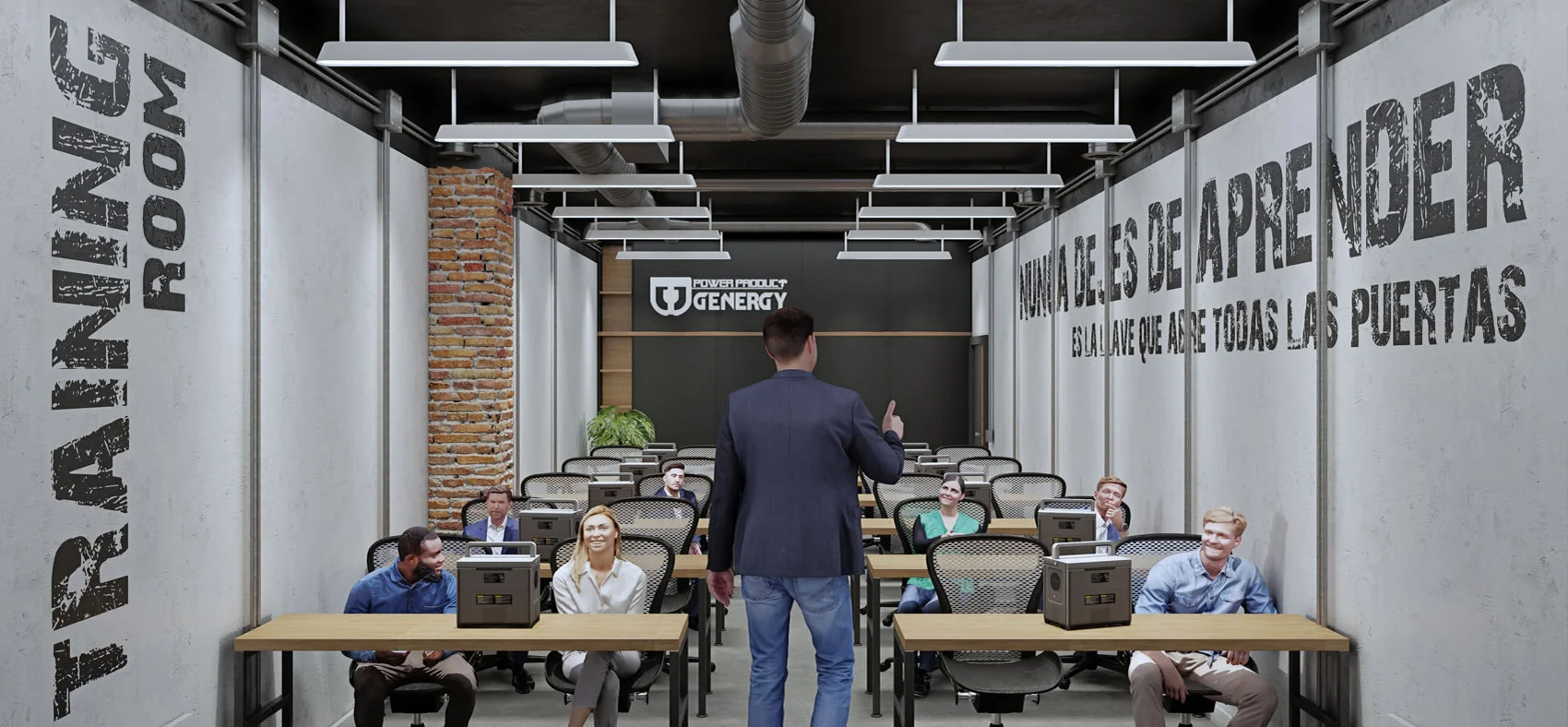
Knowledge is the basis of everything.
Permanently trained own teams
We provide training to our distributors.